Your Guide to the Manual Handling Operations Regulations 1992
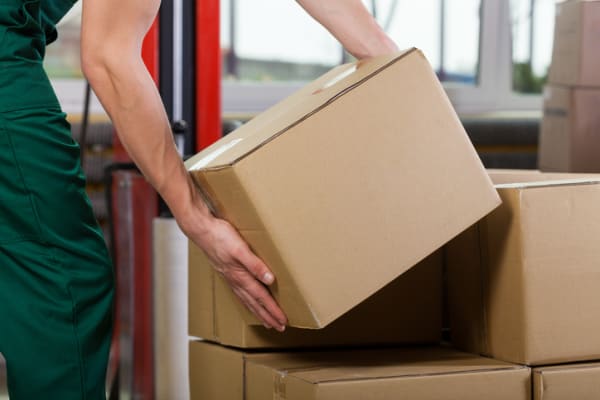
All employers have a legal duty to protect their employees from injury caused by manual handling operations. ‘Manual handling’ can refer to a range of tasks, primarily lifting, transporting or carrying objects.
Knowing and following the current manual handling regulations is also good business sense. Musculoskeletal injuries (MSIs) account for more than a third of all workplace injuries, according to government statistics – and many are caused by incorrect manual handling.
This is clearly demonstrated by the fact that 47% of injuries affect the upper limbs and neck and 38% the back. MSIs are the third commonest cause of absence from work, with only stress and minor illnesses such as the common cold ranking higher.
Summary of the Manual Handling Operations Regulations 1992
The Manual Handling Operations Regulations 1992 (MHOR) are UK regulations safeguarding against injuries during manual handling tasks. The hierarchy of measures to reduce the risks include:
Avoid manual handling where possible.
Assess risks, considering load weight, distance, frequency, posture, surface, and worker capability.
Mitigate risks through training, equipment, or process changes.
The regulations apply to any activity that involves lifting, lowering, carrying, pushing, pulling or otherwise moving a load by hand or by bodily force.
The Manual Handling Operations Regulations 1992 Hierarchy of Controls
The MHOR set out a hierarchy of controls that employers must use to reduce the risk of injury from manual handling. A summary of the hierarchy is as follows:
1. Avoid hazardous manual handling operations so far as is reasonably practicable. This means that employers should try to find ways of doing the job without having to lift, lower, carry, push, pull or otherwise move loads by hand or by bodily force.
2. If it is not reasonably practicable to avoid hazardous manual handling operations, then employers must assess the risk of injury. This assessment should consider the following factors:
- The weight of the load
- The distance the load has to be moved
- The frequency with which the load has to be moved
- The awkward posture that has to be adopted to move the load
- The surface on which the load has to be moved
- The physical capabilities of the people who will be moving the load
3. Once the risk has been assessed, employers must take steps to reduce the risk of injury so far as is reasonably practicable. This may involve providing training to employees on how to lift and move loads safely, providing suitable equipment, or changing the way the job is done.
Employers must also ensure that employees are aware of the risks associated with manual handling and that they are following the correct procedures. Employees have a responsibility to use the equipment and procedures provided by their employer and to report any concerns they have about manual handling.
The MHOR are enforced by the Health and Safety Executive (HSE). If an employer fails to comply with the regulations, they could be prosecuted by the HSE. Penalties for non-compliance with manual handling legislation can include fines and imprisonment.
What do the Manual Handling Operations Regulations 1992 cover?
The Manual Handling Operations Regulations 1992, which were updated in 2002, apply to the broadest possible definition of manual moving and handling activities, including not only boxes, cases and other inanimate objects but also people and animals.
Regulation 4(1) of MHOR (the usual abbreviation for the manual handling regulations) sets out a hierarchy of simple measures, designed to reduce the risks:
Avoid hazardous manual handling operations so far as is reasonably practicable
Assess any hazardous manual handling operations that cannot be avoided
Reduce the risk of injury so far as is reasonably practicable.
What does the Manual Handling Act mean by 'reasonably practicable'?
HSE guidance on the Manual Handling Operations Regulations 1992 defines reasonably practicable as "balancing the level of risk against the measures needed to control the real risk in terms of money, time or trouble". It clarifies this by adding that "you do not need to take action if it would be grossly disproportionate to the level of risk."
This makes it essential for employers to conduct a risk assessment, as it is the only way to judge what is reasonably practicable - and what is not.
Everything starts with the Risk Assessment
As with all health and safety issues, a risk assessment is the primary requirement – as prescribed in the Management of Health and Safety at Work Regulations 1999. Employers’ risk assessment responsibilities expressly include manual handling tasks. Phoenix can help you as an employer to comply with the manual handling regulations in a number of ways, including conducting manual handling risk assessments for you and providing a range of manual handling awareness training courses, suitable for employees at different levels.
What are the Manual Handling Laws Employers need to know?
A list of legislation that relates to moving and handling in the workplace is surprisingly short:
The Manual Handling Operations 2002, which updated the original manual handling regulations, but didn't change the fundamental employer responsibilities. The correct title for this updating legislation is The Health and Safety (Miscellaneous Amendments) Regulations 1992.
Complying with the current manual handling regulations is a key aspect of employers' general responsibilities for health and safety in the workplace under the Health and Safety at Work etc Act 1974.
The Management of Health and Safety at Work Regulations 1999 require employers to carry out risk assessments, make arrangements to implement necessary measures, appoint competent people and arrange for appropriate information and training to be provided for all aspects of workplace health and safety, including manual handling.
Employees also have health and safety responsibilities
Employees have general health and safety duties under the manual handling operations regulations to:
Follow appropriate systems of work laid down for their safety
Make proper use of equipment provided for their safety
Co-operate with their employer on health and safety matters
Take care to ensure that their activities do not put others at risk
To safeguard staff welfare, we recommend our online manual handling health and safety course. The course takes approximately 40 minutes and is suitable for employees across a range of industries.
For managers overseeing workforces who have to frequently employ manual handling, we offer the IOSH Managing Safely Course, which will help you ensure employees are working safely.
If you are interested in studying our NEBOSH Certificate or Diploma courses, visit our NEBOSH Online Courses training section.
For up-to-the-minute advice on risk assessments, staying compliant with the law and protecting employees performing manual handling tasks, contact the Phoenix team.